Finally, an industrial-scale facility for testing new, clean hydrogen technologies
Published at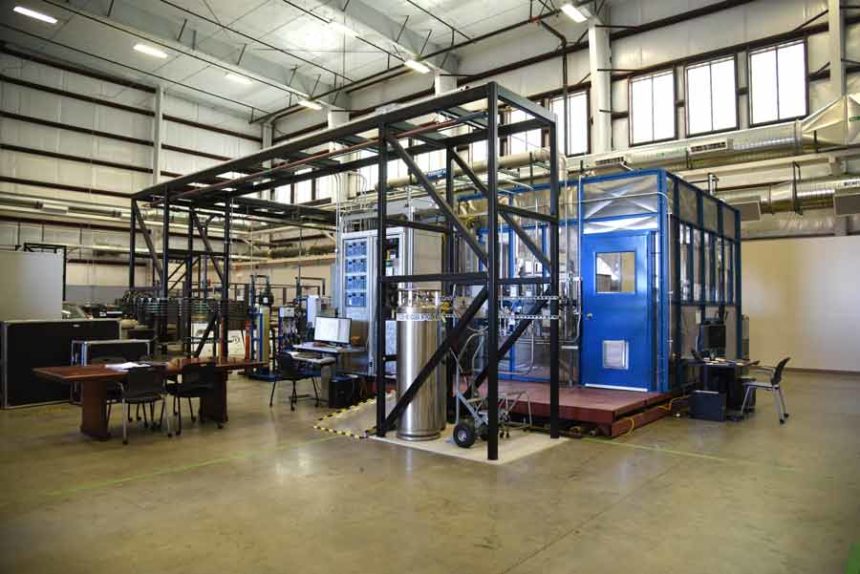
IDAHO FALLS – Hydrogen, the simplest and most abundant element in the universe, is vital for any number of industries, from fertilizer production to metal manufacturing and from petroleum refining to chemical synthesis.
Hydrogen is also an excellent way to store energy for electricity generation or to power vehicles. But the most common way to produce hydrogen — steam methane reforming — relies heavily on natural gas and produces carbon dioxide, one of the chief greenhouse gasses contributing to climate change.
To wean hydrogen production off fossil fuels, U.S. companies are investing in technologies that use energy produced by low-emission nuclear reactors and renewable energy sources to produce hydrogen. One of those technologies, high-temperature electrolysis, can use electricity to split the steam emitted from a nuclear reactor into hydrogen and oxygen.
With 20 years of support from the U.S. Department of Energy, a team at Idaho National Laboratory has developed a new capability dedicated to helping U.S. companies scale up production and drive down costs of hydrogen produced by high-temperature steam electrolysis technologies. In particular, INL’s hydrogen laboratory is designed to support the development and testing of steam electrolysis technologies and systems from multiple companies, proving their performance and safety.
INL’s team features leading materials scientists and engineers in the field of electrolysis and hydrogen fuel cell development.
“INL is the premier laboratory for demonstrating high-temperature steam electrolysis in the nation,” said Shannon Bragg-Sitton, director for INL’s Integrated Energy and Storage Systems Division. “If you want to demonstrate high-temperature, highly efficient hydrogen generation, you come to Idaho.”
ADVANTAGES OF HIGH-TEMPERATURE ELECTROLYSIS
Producing hydrogen with high-temperature steam electrolysis has a number of advantages: it requires no natural gas, it produces no carbon, and it achieves higher efficiencies than the low-temperature electrolysis options.
Besides nuclear reactor thermal energy, steam can also be generated from the waste heat emitted by other industrial sources, which could reduce both the energy needed from the nuclear reactor and the cost of hydrogen.
Producing hydrogen from high-temperature steam and electricity is also highly efficient.
“High-temperature electrolysis has a 20 to 25% higher efficiency than low temperature electrolysis (generating hydrogen from electricity and water) — especially if you use the high-temperature heat and electricity supplied by a clean energy source like nuclear,” Bragg-Sitton said.
ENABLING COMPANIES TO TEST TECHNOLOGIES
INL is the research arm and testing laboratory for several companies developing high-temperature electrolysis technologies.
The hydrogen team has set up several hydrogen production test platforms at INL’s Energy Systems Laboratory that enable companies to evaluate their technologies, especially the stacks of solid oxide electrolysis cells — devices where a catalyst facilitates the electrochemical reaction that converts electricity and steam into hydrogen.
“In the past, technology had a hard time making the jump from the lab to the commercial and industrial space,” said Micah Casteel, a senior mechanical design engineer.
INL’s test platforms can help lower the risk of such jumps, making it possible to get new technologies into the marketplace faster, he said.
“We verify system performance — that it does what it says and that it is safe and efficient to operate,” Casteel said. “If you’re going to invest in megawatts and gigawatts of a new technology, you want to be able to verify, ‘Yeah, it really does what they say.’”
Inside the laboratory, the 25-kilowatt electric test system enables researchers to test stacks of solid oxide electrolysis cells under various operating conditions, including long-duration operations with repeating on-off cycles.
“Companies want to know when they install a hydrogen production system, is it going to last 10 years or 20 years, and how much degradation in performance can they expect over time?” Bragg-Sitton said.
Behind the laboratory, a large-scale 100 kW electric system is operating. Researchers plan to install additional systems ranging from 30 kW to 250 kW within the next year. (A 100-kW system produces about 60 kilograms of hydrogen per day, the equivalent of about 60 gallons of gasoline.)
“Some companies can’t test their full-sized systems in-house because they don’t have a facility large enough,” Casteel said. “That’s the role we’ve positioned ourselves to be in — capable of testing full-scale modules that would be used in an industrial installation.”
“We have plans to program our system to emulate a nuclear power plant or a chemical refinery, so when high-temperature electrolysis systems are installed in those places, the customers know what they’re getting,” he continued.
Eventually, researchers hope to co-locate a hydrogen production system near a next-generation nuclear reactor planned for demonstration and operation at the INL Site. Demonstrating an integrated nuclear energy and hydrogen production system could accelerate distributed, on-site hydrogen production at refineries, fertilizer plants, steel mills and other hydrogen consumers.
The testing helps industry reach the DOE goal of producing hydrogen for less than $2 per kilogram by 2026, as well as the Biden administration’s 2021 Earthshot goal of reducing the cost of hydrogen to $1 per 1 kilogram in one decade. When these cost targets are reached, electrolysis will be competitive with steam methane reforming at current prices of natural gas.
(For comparison, in the U.S., current electrolysis technologies produce hydrogen anywhere from $4 to $115 per kilogram, whereas hydrogen produced using natural gas costs between $1 and $2 per kilogram depending on the purity of the hydrogen.)
GATHERING HIGH-QUALITY DATA
All of the test systems include extra instrumentation to measure parameters such as temperature and pressure so companies can gather high-quality data during their systems’ trials. The tests help to develop control systems and train operators who will run commercial plants.
“We’re making sure it meets codes and standards and that there’s adequate contingency planning and testing in real-world conditions,” Casteel said. “At our test platform in Idaho Falls, we have negative 5-degree Fahrenheit weather, high wind and hot weather— all in the same week sometimes.”
Aside from helping companies validate the performance of their electrolysis and fuel cell technologies, these systems could eventually help INL reach its goal of net-zero carbon emissions by 2031 by producing hydrogen to partially power the lab’s fleet of 80 employee coaches, as well as other applications.
In the end, INL’s contribution to hydrogen research and development could go a long way toward decarbonizing some industries that might otherwise have a hard time reducing carbon emissions. For example, hydrogen can be combined with carbon dioxide to ultimately produce low-emissions synthetic fuels for the aviation and heavy transport industries, drastically reducing their carbon footprints.
Clean hydrogen, when used in a process called direct reduction of iron, could reduce carbon emissions for steel manufacturing by as much as 90%.
“The goal is to ramp up the production scale of high-temperature electrolysis,” Bragg-Sitton said. “When you start producing larger quantities, costs go down. Eventually, producing hydrogen with high-temperature steam could cost less than steam methane reforming.”